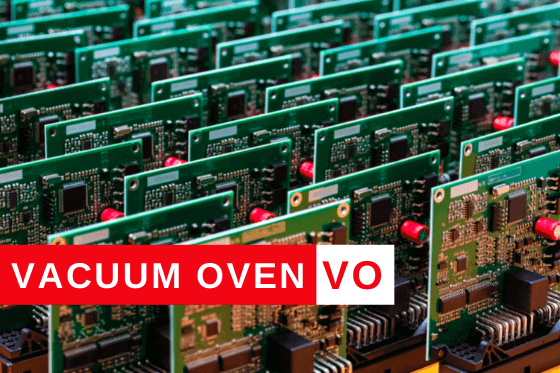
Vacuum Processing – common practices in several industries
Vacuum ovens are a very common piece of equipment used in a wide range of industrial/laboratory applications. Three of the main industries that utilize vacuum technology are electronics, medical, and aerospace manufacturers. All of these industries rely on vacuum ovens to remove substances from samples without overheating. During the manufacturing process of industrial components, there are solvents, epoxies, lubricants, and other chemicals that can travel with the parts. By reducing the pressure, these chemicals can transition to the gas phase and escape — or “off-gas” — at lower temperatures. Below is a look at some of the science and specific uses for vacuum ovens in different industries.
Electronics
During printed circuit board manufacturing, vacuum processing is used to cure coatings and dry the electronics. The boards are made of heat-sensitive plastics that would quickly shrink in a standard convection oven. By using a vacuum oven and reducing the pressure, epoxies can cure and water can be pulled out at nice, low temperatures. This allows the boards to be clean and dry as they move to the next phase of production. A bonus feature of a vacuum oven is drying wet electronics, such as a cell phone. Anything from a phone that was dropped into a toilet or a keyboard that was the victim of a spill can be dried quickly and at a low temperature in a vacuum oven.
Medical Devices
Even in clean manufacturing environments, product components are full of trapped chemicals. Some of these chemicals can be harmful to people if introduced into the body. Devices such as heart valves, artificial joints and catheters require vacuum processing prior to implantation. These devices are typically made of heat-sensitive resins that would be damaged in a high-temperature convection oven so vacuum processing is a must. All of the trapped chemicals in the devices would be left to leech out into the patient’s body if not first processed under a vacuum.
Aerospace
The aerospace industry relies heavily on vacuum technology for research and manufacturing. Before sending items into space, engineers need to know how they will behave in that vacuum. Vacuum vessels assist aerospace engineers by simulating the high vacuum environment of space so that the behavior of different widgets can be assessed prior to launch. Self-assembling satellites are frequently launched into space and then left on their own to unfold into the final array. The research and engineering that makes that possible require simulated space environments — such as a vacuum oven — to perfect the process. Check out the “V0 Cool” by Memmert.
Meanwhile, everything that is going into space must be cured in a vacuum oven prior to launch. At atmospheric pressure this may not be an issue; however, as soon as a craft full of thousands of unique components is launched into space, those chemical substances all begin to off-gas. As these chemicals are released, they can mix and react. The reactions can cause fire, condensation, or corrosion on the spacecraft. In order to prevent this, everything from wire harnesses to upholstery must be processed through a vacuum oven.
Important!! Get the Heat to the Product:
Evenly heating samples in a vacuum oven is much more challenging than in a convection oven. In a vacuum, operators can’t rely on warm air circulating around the oven heating everything nicely. Driving heat through a vacuum requires a lot of energy, thermal conductance, and precise control. The most direct way to heat the product is by contact with a thermal-conductive surface like a solid aluminum shelf. For efficient and affordable heat transfer in a vacuum oven, aluminum is the best choice for shelf construction. Stainless steel is an alternative to working with highly corrosive materials/substances.
We look forward to working with you concerning your vacuum equipment requirements.